|
马上注册,结交更多好友,享用更多功能,让你轻松玩转磨削论坛
您需要 登录 才可以下载或查看,没有账号?注册会员
×
1 前言
: r. @- d" j$ \% B7 g+ G世界上的一切财富都是人力资源开发自然资源的产物,其中制造业占有重要的地位,它既能创造财富,又是污染的源头。据美国工业有害废物来源统计表明:金属加工业占工业废物来源的5% ,排第4位。其中传统加上所使用的切削液给环境造成了严重的污染。可持续发展呼唤绿色制造,清洁生产需要绿色加工。本文主要利用绿色于加工技术之一——亚干式切削对几种金属材料进行切削加工试验,并探讨该切削加工方法的机理及优势。
+ m, @8 K. }8 G, o% @0 c$ q1 G2 试验方法
5 l8 k9 D0 K& o% L9 p0 l
: r, {9 \1 \3 V, M8 V- 试验材料
" |2 ], L, a4 q
- 被切削材料分别选用45钢,26HRC,D=75mm;CCr12, 58HRC, D=76mm;Cr12, 52HRC, D=82mm。 % u2 u) G! B' D( |! ]% |5 i Q( |
- 45钢是中碳钢的代表,其特点是切削性能好;GCr12是高强度轴承钢的代表,其特点是耐磨损,切削过程中所需功率大,刀具磨损严重;Cr12的特点是具有较高的抗拉强度,导热率低,切屑内的温度梯度高,加工中切屑一刀具接触表面温度高,极易加剧刀具的扩散磨损,加之其粘性大,切屑极易粘着刀尖,影响加工质量,影响切削过程的稳定性。
0 ~& b O, p! D. G6 x( C; W
- 试验装置 8 I% R# m' w/ q" T; g
/ {- Q. T! o! r* @2 P, q
- 机床及测量仪器:机床(CA6140车床);测力仪(Y60-3A )、光线示波器(SC16型)、X-Y函数记录仪(CZ3-304,精度0.5mm,规格:25mm×3Omm);自制刀具—工件热电偶,电压表(Pz26b);(BCJ-2型表面粗糙度检测仪;WNY-150医用测温仪, 4 O; ?# P8 t* ~$ g- z7 y
- 冷风发生装置:自制设备,温度最低可调至-35℃ 。 p5 U* K! e4 n c2 m. z
- 刀具:车用机夹刀片。切削GCr12时使用德国产SNMM120408-NR7 WAP3O(测切削力时); SNMM150612 WAP20 (测切削热时)。切削45钢时使用国产YT15 SNMM12 0408(测切削力时),YT15 SNMM150612 (测切削热时)。切削Cr12钢时使用国产YW1(测切削力时),YT15(测切削热时)。
0 S* E; b& z. m- M
5 W+ Q) H4 @* o) L( \, l1 ~2 N: ]2 o! o" J; n4 U& i. h2 W* t9 w3 f% G, G. U" i, b* V& A4 W" A- k
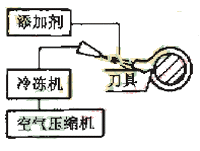 图1 试验装置 |
6 B" u ` Q1 f; s - 切削试验方法
. S" N: `% W1 S0 L4 ]% H9 ~
- 本试验采用的试验装置如图1所示,即将压缩机产生的压缩气体送至冷风发生装置,并由仪器、开关调节到所需温度,再由喷嘴喷射到刀具前刀面和切屑之间,从而起到排屑和冷却切削区的作用。而亚干式切削时,添加剂以滴注方式随冷风带人前刀面和切屑之间。
: g1 w) f) \9 w* v; c, J' I) `( x% N
- 本研究均以连续切削为研究对象,所有相同材料,相同类别的试验均在同一根试件上完成;在切削稳定性试验时采用同一根材料。分段连续切削完成,以增加同类试验的可比性。
" I; x( w0 q$ K, o0 L
- 试验内容
& y! _1 O! K8 z- z
- n Z4 |2 i- V: D- 切削GCr12时,取ap=0.75mm, f=0.1mm/r, 得图2。 . g8 b0 R$ l7 ]# h, d. u2 t
- 切削GCr12时。取V=49m/min , f=0.15mm/r, 得图3。
4 I" a9 W4 J3 u I# I" F) |' }0 L1 X+ ?- @! U. p& s p) o* ]. d9 M2 k; k' d- s" W3 e0 U" H% C9 Z6 }& S* d9 z: R( B. _5 ^* R% K6 [7 _; L4 W) r; R+ G- ]* S; O n, S$ m$ W$ _& @& e: K+ R9 Q P; M' ~# x. }3 b0 f
$ u' ?' Q( a1 r7 ~4 _& A9 p
/ x( _0 Q/ y4 i3 }# n" M7 q& r
1.自然冷却 2 风冷(-23℃) 3.烧注冷却 图2 切削GCr12时三种冷却方法切热与切削速度关系 |
/ y; W; o+ o* w1 R. a : r% B' B9 l2 Q! X( m* v- @' D
1.自然冷却 2 风冷(-23℃) 3.烧注冷却 图3 切削GC12时三种冷却方法切削力比较 |
, ]" ?' ~/ \. v 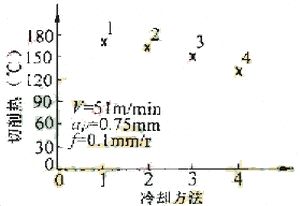
t# {. b8 a# o1.自然冷却 2.浇注冷却 3.风冷(-23℃) 4.亚干式 图4 切削Cr12时不同冷却方法切削热比较 |
% u: F" [9 ?2 B1 Y3 n4 C% K8 @9 Q 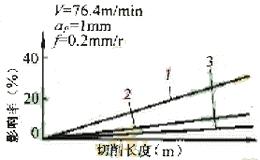 ' W- b5 L5 E$ A E) `8 Z
1.自然冷却 2.风冷(-18℃) 3.亚干式 图5 切削GC12时不间冷却方法对刀具磨损和尺寸精度的影响 |
0 G8 t$ A: A9 Y* `6 R4 o - 切削Cr12时,取V=51m/min, ap=0.75mm, f=0.1mm/r,得图4。
" R! D8 c1 D% i6 |3 t1 t" Q4 Q! K2 I
- 切削CCr12时.取V=76.4m/min,ap=1mm,f=0.2mm/r,得图5。 & |1 ~- A z1 E
- 切削以CCr12时.取V=52m/min,ap=1mm,f=0.2mm/r,得图6。 , P- P: c! t$ r D5 \0 t
8 B/ p6 K' f/ T6 s% |& q% j" p; I: D) `5 U. }7 r/ G1 B* Y* j6 q4 ]2 |6 i' g6 ?' o% H, J4 j% I! Q9 w( m4 d. S
* A7 P& G: t' w. e
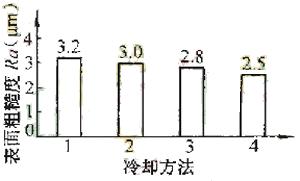 ! r0 \& m& m+ x; p( C+ X! N( P
1.自然冷却 2.-14℃冷风射流冷却 3.亚干式方式Ⅰ(从前刀面射流)4.亚干式方式Ⅱ(从前、后刀面同时射流) 图6 切削Cr12时表面粗糙度Ra值与冷却方法关系 |
7 \0 Y! \# e7 {
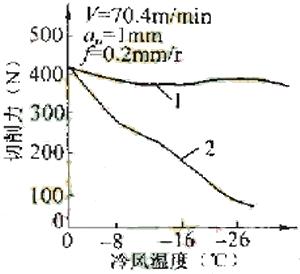 ( ]. g& B& w' u5 |4 v
1.风冷 2.亚干式 图7 切削45钢时冷风冷却切削力的比较 |
8 P( I/ j' C/ s! T5 g* C - 切削45钢时.取V=70.4m/min,ap=1mm,f=0.2mm/r,得图7。
1 A2 }0 \5 H1 B5 M3 试验分析与理论探讨
- a5 M0 e4 w* o; Z# k _7 e: f/ m: }- f+ v) d
- 切削力与切削热
( S$ l6 E- p9 w# V0 j: `
- 由图2可以看到,在切削低温区,浇注冷却的效果好于风冷;而在高温区泛风冷的效果好于浇注冷却。由图3可以看到,在自然冷却、风冷(-15℃)和传统冷却的切削中,在工艺参数相同的条件下,自然冷却切削力最大,亚干式切削力最小。由图4可知,在自然冷却、浇注冷却、风冷(-23℃)和亚干式切削中,切削热依次减少。对此可分析如下:
2 M: ]. `; Y7 j3 P( q/ g8 @5 y
- R( k/ F0 b9 t8 s% W& F
- 在切削用量相同,刀具几何参数一致的情况下,影响切削力的最主要的因素是工件材料、切削时的冷却状况和刀具磨损。其中工件材料的物理机械性能及状态影响最大,材料的强度、硬度越高,则创剪应力)越大,从而切削力越大。而本试验工件材料、刀具材料均一致,在各切削参数相同的前提下,切削力应基本趋于一致。因此,试验结果不一致应归结于冷却方法的不一致,是不同的冷却方法改变了切削区材料的某些性能以及相应的刀具磨损状况。研究表明:低温切削时体心立方晶格材料易发生低温脆化。此时材料的机械性能受到金属内部晶格位错影响,在低温下金属内部位错热能低,其塑性变形应力比高温下抗力大,因而能提高材料强度;而低温脆性是由孪生引起的龟裂所产生的。体心立方晶格金属引起滑移所需屈服应力随温度急剧增大,但孪生应力因温度不同而产生的变化不大因此,低温下孪生应力比滑移应力小,低温脆性是由孪生优先发生的。由此可见:低温强风冷却引发被切削材料的低温脆性是切削力小于其它冷却方法的主要原因;同时低温降低了切削热温度,保护了力具的切削性能,也从另一侧面延缓因刀具磨损引发切削力增大的趋势。 $ B g, ~( Z$ c+ K8 t/ f5 x* d
- 在冷风冷却切削中,亚干式切削的切削温度低于一般的冷风切削,这应归功于亚干式切削中添加剂的润滑作用。金属切削中所消耗的全部功转化为热,而热主要产生在第一变形区和第二变形区;工件材料在第一变形区受剪切时,随着刀具相对于工件的连续运动,剪切应力增大,并伴有加工硬化现象,在整个切削宽度上存在着极大的温度梯度,通常在600℃左右.切削力也由此大大减小;随着切削在第二变形区的继续进行,切屑沿前刀面流出,受到前刀面的挤压和摩擦作用,使紧挨刀具前刀面的切屑温度最高可达750℃左右;在没有润滑液、切削温度很高的情况下,前刀面与切屑是粘结摩擦或内摩擦;当润滑液渗到切屑、刀具与工件的接触表面之间以后,粘附在金属表面形成润滑膜,以此减小切屑与刀具、工件之间的摩擦系数、减轻粘结现象,以达到减小切削力和减少切削热的目的。另一方面,按照切削方程式f=p/4-b+a(f为剪切角,b为摩擦角,a为刀具前角),减小摩擦系数意味着夕变小,协增大,从而使前刀面与切屑的接触长度减小,减少了摩擦,因而降低了切削温度,这种效果是切削液冷却和亚干式切削所共有的。但在高压、高温下油膜厚度会减薄,并部分蒸发,金属表面的凸凹不平极易破坏油膜,使之趋向于边界润滑。因此切削过程中润滑介质的润滑作用取决于润滑介质的润滑性能与其渗透性、成膜能力等:亚干式切削过程中切削区材料有低温脆性、添加剂的渗透作用强,使之较切削液冷却时的切削温度更低。
9 {* b& X( f: v+ u" F - 刀具磨损和加工精度
% a/ }+ r1 a& }( `9 |
- 从图5可以看到,切削方法对刀具磨损和尺寸精度影响以亚干式切削、风冷、自然冷却切削的顺序由小到大,其中亚干式切削刀具磨损小,加工精度高;自然冷却切削刀具磨损严重,尺寸精度低。可作如下分析:
- ?" X& f: u% b% @
' p" \) _) u( O5 `! b
- 在切削加工中,影响刀具寿命的最主要因素是切削点的切削热,切削热温度升高会使刀具切削刃软化,从而加速刀具磨损。冷风冷却导致切削区工件材料的低温脆性,减小了切削力,降低了切削温度,防止了刀具软化;亚干式切削不仅防止了刀具的软化,而且减轻了刀具、切屑和工件接触面之间的摩擦,因此刀具磨损最小。
$ F! o# E; l' M
- 影响被加工零件的尺寸稳定性的因素,主要是切削过程中工件温度、刀具磨损在一个切削过程中的变化量。工件变形大,刀具磨损快.零件的尺寸稳定性就差在上述儿种冷却切削中,亚卜式切削时切削温度最低,切削力最小,刀具磨损也最少,因此零件的加工尺寸稳定性最好:经研究,亚于式切削时的尺寸误差是自然冷却切削尺寸误差的5.5% ;风冷是自然冷却的38% ;在相同工艺条件下,自然冷却的刀具磨损值VB=1.2mm,而风冷仅为0.42mm。由此可见亚干式切削能延长刀具的使用寿命,维护被加工零件的尺寸稳定比,有助于精密和自动化加工。
5 u J. C1 f" ^3 ^( x% E( U" E3 e8 U
- 被加工零件的表面质量 5 r6 D p$ R# `
- 图6显示了几种不同冷却方法切削情况下,对应被加工零件的表面粗糙度值的比较,其中亚干式切削零件的表面粗糙度值小于风冷,而风冷又小于自然冷却。同样是亚干式切削,如果将从前刀面射流冷却方式Ⅰ改为前、后刀面两个方向射流冷却的方式Ⅱ, Ra值就更小这说明冷却方法、方式的不同,其加工表面的质量也是不一样的:从机理上讨论这一现象,可以认为:减轻切屑、刀具与被加工表面之间的摩擦状况;减轻切削区材料的变形程度、切屑与前刀面的粘结;抑制积屑瘤就可以提高刀具的耐用度,减小工件表面的Ra值,提高零件加工的表面质量。
! n# {; ]/ u% M8 I' n) D - 冷风冷却性能 , X$ w) k* S( ~& H3 K; l2 M5 g
- 图7给出了相同工艺条件下冷风冷却、亚干式切削在不同冷风温度下的切削性能对比。由图可见:随着冷却介质冷风温度的降低,切削力都在减小,但亚干式减小得更决。由此得到两点启示:
; r+ o4 K& s5 X F
7 U1 a2 U6 Z. x) c% B `4 L- 这种现象和传热的基本理论是一致的,可以通过三种途径,即提高传热系数、增大换热面积和温差,来强化换热和传热过程。在本试验中随着冷却温度的降低、温差的增大,冷却效果也愈显著。 5 o, d/ D9 M* p% T- s2 ^
- 亚干式切削时的切削力曲线下降更快,说明亚于式切削在引发材料低温脆性、减少摩擦、保持刀具切削能力等诸多方面都是有益的,因而诸多因素的综合作用效果比单因素作用效果好。但是应该从成本、效果等多方面进行综合优化。
8 g, [6 _, h& ]* M' x2 C
4 结论! }, a2 A* p; ~, L2 k o5 {2 ^+ ^. Q
0 j/ B. n! X( Q* b* n% O- 亚干式切削、冷风冷却切削是一种较优的冷却切削方法,随着切削热、切削力的上升其冷却效果愈显著,其中亚干式切削更为明显。 1 V: a1 P( X& P; g' f
- 亚干式切削能保护被加工零件的尺寸稳定性,显著提高刀具使用寿命,减小加工表面的粗糙度值,有助于精密加工、自动化加工的实现。 % }" B; i! y9 i+ |$ @
- 一般冷风温度越低,其冷却效果会越好;但由于诸多因素的综合作用,冷风温度与冷却效果之间并不是完全的线性关系,从生产成本、冷却效果等多方面进行综合优化还需要作进一步研究。
' g+ z: [& t: _3 a' M5 }9 x
|
|