|
马上注册,结交更多好友,享用更多功能,让你轻松玩转磨削论坛
您需要 登录 才可以下载或查看,没有账号?注册会员
×
超精密切削的主要目的是要切下一层极薄的金属层,与普通切削相比,刀具前刀面参与切削部分面积减小,而刀刃附近区域却要承担大部分的切削工作,这对所选择的刀具材料提出了更高的要求。另外,背吃刀量从几微米减小到一微米以下时,车刀的尖端会受到很大的应力作用,从而在单位面积上会产生很大的热量,使刀具尖端局部区域达到极高的温度。切削时采用的背吃刀量越小,就越要求使用的刀具耐热性能高、耐磨性强和硬度高,而金刚石刀具恰恰能够满足上述要求。因此,金刚石刀具被普遍认为是超精密加工最为理想的刀具。在超精密加工中,刀具的几何形状、振动、刀具的磨损、机床的几何运动精度和工件材料的变形等因素对超精密车削表面粗糙度具有显著的影响。
3 U" Z# P4 B* O; n+ ~! _. K( z+ i, u( e0 U8 j; e5 O5 T- n' d" Z! l0 J; ^2 s! L+ G$ k6 {/ b% M; _9 o) G' d4 f t! O3 X# ~" O Z$ ^6 s% ^7 d- ~, c! D" x
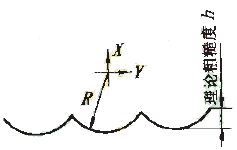 图1理想状态下形成的表面微观形貌 |
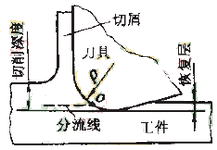 图2超精密车削模型 | . D. x9 k0 m! |2 H0 q0 [, l) ~) ~
1 刀具几何形状对表面粗糙度的影响
% b/ H8 }" K5 A r刀具的切削部分包括:前刀面、后刀面、刀具的圆弧半径及刃口半径等要素,各种要素的不同组合形成不同的切削形态。在切削过程中,刀具切削部分的形态直接影响着切削过程的稳定性和表面质量。理想状态下,采用圆弧刃金刚石刀具进行超精密车削加工软金属时,在工件加工表面形成轮廓峰和轮廓谷,它们之间的距离,被称为理论粗糙度(见图1),其大小等于f2/8R(f为进给量,R为刀具圆弧半径)。 + W5 g& h6 M9 A) n
超精密车削模型如图2所示,在超精密切削塑性金属时,主切削刃和前刀面的主要任务是去除金属,切削层在前刀面的挤压作用下发生剪切滑移和塑性变形,然后形成切屑沿前刀面流出。前刀面的形状直接影响塑性变形的程度、切屑的卷曲形式和切屑刀具之间的摩擦特性,并直接对切削力、切削温度、切屑的折断方式和加工表面质量造成显著影响。主切削刃是前刀面和后刀面的交线。实际上前刀面和后刀面的交线不可能为理想直线,而是一微观交接的曲线。该曲线的形状可以近似用与其在不同位置的法平面相交成交线的平均曲率半径来反映,称其为刃口半径r。切削时刃前区的应力状态十分复杂,应力集中造成金属中位错集中,导致金属产生塑性变形和滑移分离,一部分金属成为切屑沿前刀面流出,另一部分金属经后刀面熨压留在已加工表面。因为两部分金属运动方向不同,必然使刀具刃口前金属呈拉伸状态,拉应力使刃前区金属的抗剪能力下降,在刀刃的直接作用下,金属产生滑移分离。刃口半径越小,应力越集中,变形越容易,切削力越小,加工表面质量越好。也就是说刃口半径对切削过程有较大影响,同时对切削力、切削温度和切屑变形系数都有不同程度的影响。因此,提高刀具的锋锐程度,可减小刀具对金属的挤压力,使金属的变形程度降低,减缓金属的冷作硬化,有助于提高切削过程的稳定性,改善加工表面质量和延长刀具的使用寿命。
% j' d7 h) P. {' d# V2 l另外,切削层金属被通过分流点O且平行于已加工表面的分流线分为两部分,分流线以上的材料沿前刀面流出,分流线以下的塑性变形层被O点以下的刀刃熨压后成为已加工表面。经过熨压以后,刀刃下方的材料产生严重的压缩变形,对已加工表面质量产生直接影响。 9 e1 x9 Y5 T" K- o0 d5 U5 f
2 最小切削厚度对表面粗糙度的影响
6 Z! x0 {' d, z/ s: h/ w3 |除了机床本身的性能以外,使用刀具切削刃有效地切除工件材料时,最小切削厚度(MTC)的可控性和重复性是影响加工精度的主要因素。MTC 不仅可以反映切削刃的纳米级微观结构,还可以反映出刀具和工件材料之间的相互作用状态。最小切削厚度被定义为能够从工件材料上有效地去除金属的最小厚度。切削厚度越小,工件材料抵抗塑性变形的能力越强,刀具和材料原子之间的相互作用力越弱。当金刚石刀具刃口半径为几个纳米的特定切削环境下,最终可达到的加工精度与最小切削厚度为同一个数量级。日本学者在高稳定的机床上使用特制的金刚石刀具切削单晶铜,获得了非常微细的切屑,并使最小切削厚度可以达到$%&。最小切削厚度这个变量随着刀具的几何形状和切削条件的不同而变化。美国和日本有关专家通过实验研究发现:金刚石刀具的刃口半径r对最小切削厚度有显著的影响,当车削铝合金的时候,最小切削厚度大约为所采用刀具刃口半径的0.3~0.6 倍,这个比值随着被加工材料和切削条件(如进给量和刀具的圆弧半径)的不同而略有差异。
+ ]* g/ K4 Q( ]8 |1 [* J* Z" E5 c3 金属变形对表面粗糙度的影响1 ]0 F4 N1 o0 h( S& i
金属切削加工过程非常复杂,加工后形成的表面粗糙度与工件的材料、刀具的几何形状、润滑方法以及选用的切削深度密切相关。剪切、滑移和断裂被认为是影响切屑形成的几个主要因素。超精密切削时只要有切屑产生,就可以把该过程模型化为材料沿着与水平面倾斜一定角度的平面被刀具剪切的过程,在已加工表面上形成的峰、谷高度随刀具刃口锋锐轮廓的变化而变化。
# v" N) X; Y+ i, {% _) x$ c( S3 U2 y) ~! w% v4 o) ?1 v% @ ?; N, }% M; c. K! A& f
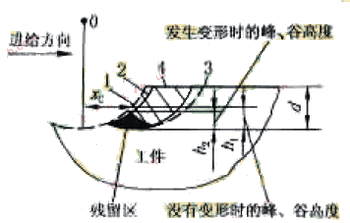 图3 切屑发生的变形示意图 |
2 O/ H( r( U1 f最小切削厚度的存在使小于一定切削深度的工件材料不能被切除。图3中所示的Xc值通常大于进给量的一半,所以不完整切屑的形成只能使表面粗糙度的值增加。对已加工表面粗糙度进行测量时我们往往会发现一种奇怪的现象,表面粗糙度的测量值有时很小,什么原因造成的呢?我们可用材料变形的观点对这个问题作出合理解释。
/ G2 w. C ?3 Q- O5 G" m图3中阴影所示部分为在加工表面上残留的区域,有关文献把它命名为spanzipfel(残留区)。虚线表示理想条件下材料去除形成切屑的边界形状,磨损的刀具进给时对被加工金属产生挤压磨光作用,使金属产生塑性变形,最终导致残留区的左边界线发生偏斜,左边界线由虚线1的位置变到实线2的位置:另外,用刀具切削金属时在已加工表面将产生弹性恢复变形,使加工表面的形状由虚线3的位置变为实线4的位置,导致残留区高度的降低、表面粗糙度值相应减小。其中残留区的高低主要取决于所使用刀具的刃口半径的大小。刀具刃口半径不同产生的弹性恢复变形不同,其对应关系如下式所示。 1 k0 B e' z! u9 A
6 C4 ~, x( t1 ^. U0 n. r2 p6 S6 U4 U7 d4 ?" [' E# v6 ?* U" W# {& Z& k+ ?2 n1 b+ e) s7 j8 _8 v6 S/ X
- q& l* |) l% a+ q4 {
7 G- n$ V- p3 A. g8 \( d: g! U' k1 r$ E) `# }. X& Z! I7 ]' ~+ N' Y0 [/ I6 o8 i3 w5 p i' F. k1 w e$ D W' r# Z, G0 B5 Q S L j5 ?& Z' U+ H0 x( l r# E$ b: T* c* F- U$ T0 P9 @5 B1 `0 K ^ |
(1) |
% F# d+ b9 b9 h8 p. y& l8 l. }
4 N' J+ r( K; l4 j4 J3 ~. v. A* I% T0 _, Y6 R8 H( U# ?' D( E
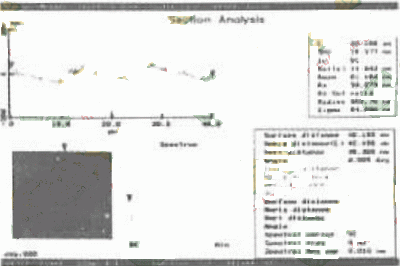 图4 加工表面微观形貌的AFM照片 |
) V* q' \1 B. C# M式(1)中S为材料恢复变形的高度,r为金刚石刀具的刃口半径,K为常数,H为材料的硬度,E为材料的弹性模量。由此可见:金属材料弹性恢复变形量的大小随着工件材料而变化,且工件表面弹性恢复变形量与刃口半径呈线性关系。加工同一种材料,采用刀具的刃口半径较小时,加工表面产生的弹性恢复变形较小:当刀具刃口半径较大时,在加工表面会产生较大的恢复弹性变形,从而降低了在已加工表面形成的峰谷之间的高度。因此,工件材料的弹性恢复变形和塑性变形,也有可能使已加工表面粗糙度值变小,这也是刀具磨损时却能加工出粗糙度值较小表面的主要原因。由测量得到的图4AFM照片也可以明显看出:金属的变形对表面形貌有显著的影响。
( V/ A+ j1 h8 q/ |( z+ u另外,工件材料对金刚石车削加工表面粗糙度有显著的影响,在一般车削加工中经常忽略材料晶体微观结构的影响,而金刚石车削中材料对表面粗糙度的影响却不容忽视。例如:某种材料的弹性模量主要依赖于单晶体的晶向,虽然铜、铝同样是软金属,但它们的硬度却有较大差异。在同样条件下切削上述两种金属时,切削状态不同,产生切削力的大小也会有所不同。另外,被加工材料的纯度、材质是否均匀以及晶体的晶向各异性都会对加工表面质量产生重要影响。 1 g& W# T4 C0 b# J# h- g5 ~) o
4 切削用量对表面粗糙度的影响
% Q4 M8 ?. |: K2 Y2 u0 R笔者通过采用回归分析方法在大量的试验和观察中寻找隐藏在随机性后面的统计规律性,根据实验目的和数据分析来选择实验点,使得在每个实验点上获得的数据含有大量的信息,在113m/min≤V≤314m/min,1.8µm/r≤f≤5.0µm/r,1.50µm≤ap≤6.00µm的条件下,建立了如公式(2)所示的金刚石车刀车削铝合金表面粗糙度的预测模型,(V:切削速度,f:进给量,ap:背吃刀量),从中可以看出各种切削参数对表面粗糙度值的影响。
' M( t4 [) R6 N1 `. m d0 J) I3 s0 k' O6 u, L# H* p4 y+ A7 e+ X3 a9 ?% e5 G. i+ f2 ~2 I c0 b6 X0 l. M
Ra=13.635V-0.1025f0.5123ap-0.0382 |
(2) |
- d3 x; F; f. U, L在上述的条件下,从预测模型可反映出:随着切削速度的增加,表面粗糙度值略微减小,这种变化主要受机床动态特性的影响。
, U2 C! B. g+ I2 E; Y) W* h当f=5.0µm/r,ap=6.00µm时,利用模型作出如图5所示的切削速度与表面粗糙度对应关系曲线,从中也可看到切削速度变化时,表面粗糙度的变化范围仅为2nm左右,因此说切削速度对表面粗糙度基本无影响。金刚石车削铜合金时也能够得到同样的结论。
| q5 k/ }% f- @0 s8 w8 W) b) E2 O0 I D4 F3 J% P3 h- l$ M/ g: ^0 B5 x) B; F9 x% Y7 y7 v2 g: `- P7 T) I7 h- N0 ?7 O! w# P( L0 D. j+ Q1 \' a. g9 p/ G- a
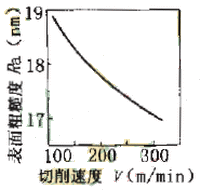 图5 切削速度和表面粗糙度对应关系曲线 |
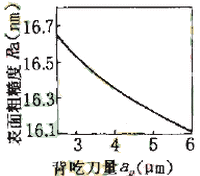 图6 背吃刀量和表面粗糙度对应关系曲线 |
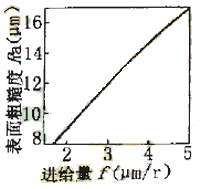 图7 进给量和表面粗糙度对应关系曲线 |
% { C% Q$ T) B1 w车削铝合金时,背吃刀量对加工表面粗糙度的影响也不显著,当切削速度为314m/min、进给量为5µm/r时,利用模型作出如图6所示的背吃刀量与表面粗糙度对应关系曲线,从中可看到背吃刀量小于6µm时,对加工表面粗糙度基本无影响。
/ f6 d j7 F" R% o5 S+ ?8 @当切削速度为314m/min、背吃刀量为6µm时,利用模型作出如图7所示的进给量与表面粗糙度对应关系曲线,从中可知小进给量可得到小的表面粗糙度值。但是由于最小切削厚度的存在,实测的表面粗糙度值往往要比理论粗糙度值大几倍。 8 N- k8 `' p- [9 K
5 振动对表面粗糙度的影响# H) F6 Y# J" i: X
尽管超精密车床具有很高的刚度,但振动仍然是影响表面粗糙度的主要因素之一。超精密机床通常都有很高的固有频率,在超精密加工过程中,实际的工艺系统是一个非常复杂的振动系统,系统中的振动使工件与刀具之间的相对位置发生了微幅变动,最终使工件表面粗糙度增大、表面质量降低。有关学者通过研究发现:机床主轴的振动、导轨的振动以及刀具的振动都具有高频率、小振幅的特征,积屑瘤、外界干扰、机床刚性不足以及高速旋转部件不平衡也会引起切削振动,最终导致加工表面微观特征的改变。 ! }- V' i" k- S
另外,切削系统中的动态效应对振动也有显著的影响。因此,必须采取必要的预防措施来减小或防止振动对超精密加工表面质量的影响。 * g8 l1 Z, ^& W+ W- w V
6 结束语
# a3 F5 R- Y% ]7 P) F本文对影响超精密车削表面粗糙度的几种主要因素进行了分析研究,指出刀具几何形状、最小切削厚度、不规则的金属变形、切削用量、振动等因素对表面粗糙度具有显著影响。本文所研究的内容对改进加工方法,研究表面几何特性与使用性能的关系,超精密车削加工中表面粗糙度变化趋势的正确识别,以及提高加工表面的质量和产品性能都具有重要的意义。 2 }9 g9 c( M! g$ h) H
|
|