马上注册,结交更多好友,享用更多功能,让你轻松玩转磨削论坛
您需要 登录 才可以下载或查看,没有账号?注册会员
×
SINUMERIK 840D数控系统仍然是当今在用的主流数控系统,是西门子数控产品的突出代表。SINUMERIK 840D提供了许多创造性的技术功能,钻削、铣削和车削加工工艺的各种标准循环等大大简化了频繁的重复性加工操作,甚至对于最复杂、最精确的应用场合,如用于加工刀具及模具的5轴坐标铣床的制造,SINUMERIK 840D也能胜任自如。本文中,作者以 600×5210沟纹辊16头螺纹在其十米数控车床加工为例,介绍了840D的CYCLE97指令在多头螺纹加工中的应用。 ; `! u% o5 a) n
在普通车床上进行多头螺纹车削一直是一个加工难点:当第一条螺纹车成之后,需要手摇小刀架并用百分表校正,使刀尖沿轴向精确移动一个螺距再加工第二条螺纹;或者打开挂轮箱,调整齿轮啮合相位,再依次加工其余各头螺纹。受普通车床丝杠螺距误差、挂轮箱传动误差、小拖板移动误差等多方面的影响,多头螺纹的导程和螺距难以达到很高的精度。而且,在整个加工过程中,不可避免地存在刀具磨损甚至打刀等问题,一旦换刀,新刀必须精确定位在未完成的那条螺纹线上。这一切都要求操作者具备丰富的经验和高超的技能。然而,在批量生产中,单靠操作者的个人经验和技能是不能保证生产效率和产品质量的。在制造业现代化的今天,高精度数控机床和高性能数控系统的应用使许多普通机床和传统工艺难以解决的问题变得相对简单了一些,而且生产效率和产品质量也得到了很大程度的保证。 , ?4 l- }1 }6 z4 _3 Y$ a3 g
一、CYCLE97指令的程序格式、加工步骤和参数说明
m& U0 U& n6 X# @& E 1. 程序格式
; Y+ ^3 ?, e6 Q+ x: X! ^ 程序格式如下:CYCLE97(PIT,MPIT,SPL,FPL,DM1,DM2,APP,ROP,TDEP,FAL,IANG,NSP,NRC,NID,VARI,NUMTH)。 1 f3 C" m9 l4 f: G. C
2. 加工步骤 6 p P5 H2 D y) }9 E& F
车刀快速移动到起刀点(由DM1、DM2、APP确定),按照IANG指定的进给切入角度和VARI指定的稳定进刀方式或者递减进刀方式开始粗车,粗车次数由NRC指定,粗车总切深由牙型深度TDEP减去精车余量FAL得到。粗车结束后,通过一次精车将FAL加工余量切除,然后,根据NID指定的次数,进行空走刀修光,最后返回起刀点,CYCLE97程序结束。当加工多头螺纹时,每一条(头)螺纹均按以上步骤车成后再开始加工下一条(头)螺纹。螺纹头数由NUMTH指定,第一条螺纹在零件端面圆周方向上切入点的相位由NSP指定,其余各头螺纹通过自动改变刀尖在端面圆周方向上切入点的相位而依次产生。 3 i- \- X' u( s2 P& \6 ~# @
3. 参数说明
0 \6 ^" O" u/ F' r PIT——螺距;MPIT——米制粗牙螺纹的公称直径,范围M3~M60(注意,PIT和MPIT在CYCLE97指令中只能选择一项输入。例如,M42粗牙螺纹,PIT项不用输入,MPIT项输入数值42;M95X2细牙螺纹,PIT项输入数值2,MPIT项则为空值);SPL——螺纹起点轴向坐标值;FPL——螺纹终点轴向坐标值;DM1——螺纹起点直径;DM2——螺纹终点直径;APP——起刀点至螺纹起点轴向距离;ROP——退刀点至螺纹终点轴向距离;TDE——螺纹牙型深度;FAL——最后一次走刀的加工余量。以上参数如图1所示。 ! `. I, T& _& ?5 Q$ e* E, k K
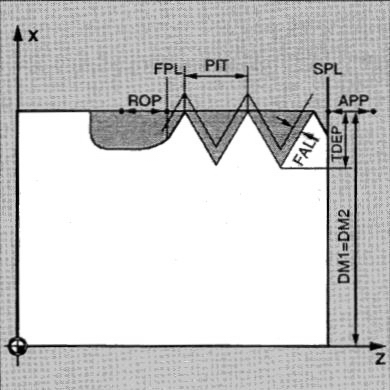 2 n& C7 q( K1 F% N; V
图1
0 g- S8 n2 S* g IANG——车刀径向进给切入角度,IANG值应小于或等于牙型角的一半(当从径向垂直切入时,IANG为0,也可以不输入数值,机床默认为0。IANG为正值,表示每一次走刀总是沿着牙型的同一侧面进给。IANG为负值,表示沿着牙型的两个侧面交互进刀。IANG为负值的情况只适用于圆柱螺纹加工,在锥螺纹加工中,无论IANG为正或负,每一次走刀始终沿着牙型的同一侧面进给),如图2、图3所示。 / r8 d8 ]4 d: k c0 t6 x& Y' d. S
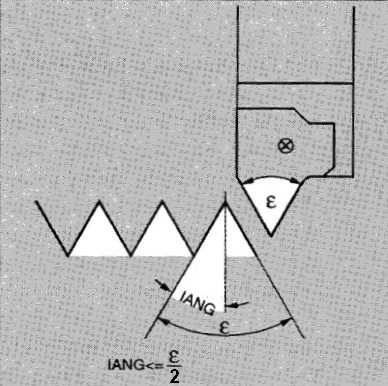 & \* }) H0 _8 ?
图2
. l5 R8 V5 L# e! u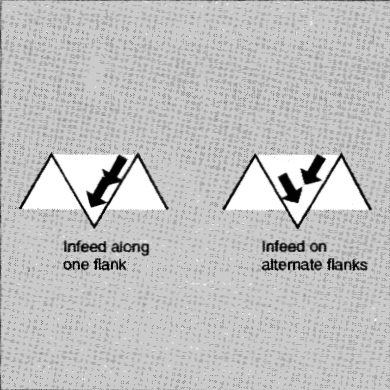 ' ~2 @: A4 }, J* z
图3 / u/ f% T2 i0 L5 C5 D; s. `
NSP——螺纹在零件端面圆周方向上切入点的相位(可以不输入数值,机床默认为0。当车多头螺纹时,表示多头螺纹的第一条螺纹在零件端面圆周方向上切入点的相位,如图4所示)。 8 X6 a2 A/ X- O9 Y. M7 v
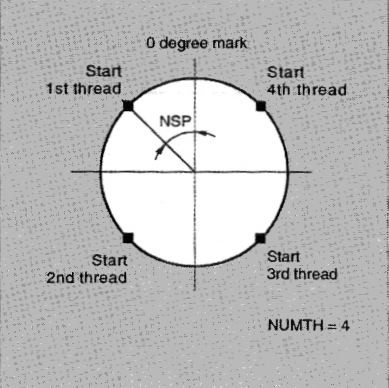 # v1 R4 O7 ], C& C9 z6 w
图4 , r# L7 W8 w7 P: u4 O( r
 . H* L5 d) y+ S2 c q( m4 P
图5 % E- J' T7 X6 F
NRC——粗车走刀次数;NID——最后空走刀次数;VARI——每次走刀进给切深的选择方式(1表示加工外螺纹,稳定进给,每次走刀切削深度相等;2表示加工内螺纹,稳定进给,每次走刀切削深度相等;3表示加工外螺纹,递减进给,每次走刀切削截面的面积相等;4表示加工内螺纹,递减进给,每次走刀切削截面的面积相等,如图5所示)。
/ f: K$ _ |2 x% U8 B+ Z NUMTH——多头螺纹的头数。当车普通单头螺纹时,可输入0或不输入数值,机床默认为0。 1 N8 u; w6 n! [# f
二、零件的结构尺寸及工艺
5 q" v. P) ?, g! V9 z 1.零件简图
( ]+ o6 |, [: H( ^ 零件简图如图6所示。
: U/ ] ? E5 g3 t: [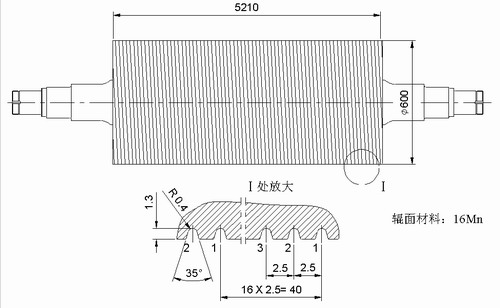
& j! v5 t& q5 C3 }. ^4 y9 t" S图6 零件简图
' C) X1 S& [3 _: B6 Y 2.工艺 ! b8 E" {1 u6 q7 x- ]
(1)刀具
0 v7 q8 j. _6 O T: m 刀杆型号为SANDVIK SVVBN 3225P16;刀片型号为SANDVIK VBMT 16 04 04-PM。 ) F) |( _! [# K% E2 h
(2)加工参数
+ u/ W9 k& A9 G 切削速度Vc=140m/min;主轴转速n=75r/min。
4 u9 x8 q1 j" s. m/ C' r0 O (3)工艺方案
R3 k- `" S( U# _5 x K7 t 考虑到辊体直径和长度尺寸较大、加工余量较大、车刀易磨损等原因,故分成粗、精加工两道工序。螺纹最终牙型尺寸和精度由精车保证。精车时加工余量为0.1mm,分两次走刀,一次走刀切除剩余加工量,第二次空走修光。粗车时总切深为1.2mm,每刀进给切深0.12mm,走刀次数=10次。
! ^+ T3 r6 h* ~7 E; Y: i4 X (4)每次走刀进给切削深度的方式选择
2 L9 y5 d+ R& v 由于所选机夹刀具是非标准螺纹车刀(35°牙型角,非标),该刀片前角、后角偏大,且无螺旋升角,导致切削力大,刀片强度差,所以采用稳定进刀方式,即将牙型深度分成若干次走刀完成,每刀进给切深相同,这样可获得良好的切屑控制,并避免按递减方式走刀时所产生的第一次走刀切深过大、易崩刃等问题。 : p* K& @/ y( c
(5)每次走刀进给切入角度的方式选择
: t- [) c, \3 `5 X+ G 精车时切削量小,可采用径向垂直进刀,以保证螺纹牙型准确,精度高,并可获得好的表面粗糙度。粗车时切削量大,如果采用径向垂直进刀,考虑到两条刃同时切削,因为辊体壁厚较小(δ16mm),辊子刚性较差,加工中易产生振动;径向垂直进刀会形成V形切屑,切削热量大,刀尖圆角易过载,所以我们采用改进式侧向进刀。这样可获得扁平卷曲切屑,排屑良好,切削热量小,刀具寿命长,如图7所示。
) w+ O2 F+ z3 V" A; A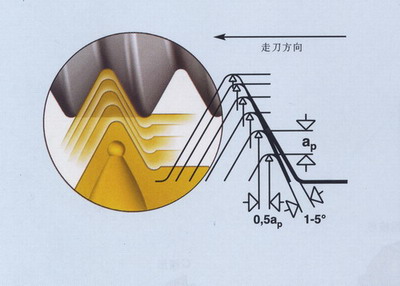 ( b( z& w2 G& M" D8 ?* u6 `- L
图7
- R1 e: R, X. N三、编程
! p* S- t' n: D3 M 1.CYCLE97各项参数的设定 5 h2 k# n5 ^( G8 W: q8 o& O
PIT,多头螺纹的螺距值就是单条螺纹的导程,按图6取40。MPIT,空值,不用输入。SPL,按图6取0;FPL,按图6取-5210。DM1,按图6取600。DM2,按图6取600。APP,起刀距离一般按3~5螺距,为了便于检查刀具磨损情况和换刀,可适当放大,这里取100。ROP,退刀距离一般按1~3螺距,应参考图纸中退刀槽宽度尺寸确定,此处取30。TDEP,螺纹牙型深度,粗车程序中取1.2,精车程序中取1.3。FAL,最后一次走刀时的加工余量,根据前述的工艺方案,实际加工余量是在精车程序中切除,所以在粗车CYCLE97和精车CYCLE97程序中均取0。IANG,径向切入角度,粗车时采用改进式侧向进刀,取IANG=15,如图7所示,精车时按垂直进刀,取0。NSP,第一条螺纹在辊体端面圆周方向上切入点的相位,取0。在实际加工中可根据需要改变该值,以指定车刀加工第几条螺纹,如图8所示。VARI,如前所述,选择稳定进给方式,取1。NUMTH,螺纹头数,取16。所有参数列于参数列表中。 & A6 ? j: }' J- E; P- A
2.程序
/ Z$ e" q N/ y5 T; Q (1)粗车程序 $ M/ P5 M' g" I/ a1 J# D
CYCLE97(40, ,0,-5210,600,600,100,30,1.2,0,15,0,10,0,1,16) # b) g8 h8 O) u/ b8 Y$ x
(2)精车程序
% L# X: W: ~3 v- Y* e( N" ? CYCLE97(40, ,0,-5210,600,600,100,30,1.3,0,0,0,1,1,1,16)
, W3 h' y# C8 V- S" Q
. b$ a1 j# W- b参数列表 & _9 A: v& Z% e* _1 d5 H
四、注意事项与常见问题的解决 & T+ X. Y+ F0 X; R; z
1.刀具磨损与打刀
2 A s) t7 z* H! l 数控车床加工螺纹时,程序一般可以通过试车调整而不断得到优化,最常见的问题是刀具磨损和打刀。为提高刀具使用寿命,防止打刀,应注意以下几点:
' F' h. f/ ^% h. {6 d; \1 @ (1)在车螺纹前的精车外圆工序,应保证一定的尺寸精度、圆度、圆柱度和表面粗糙度,并检查辊面是否有焊接裂纹、夹渣等缺陷,以保证加工余量均匀,车削平稳。
4 e1 f& a( Z. ? (2)走刀进行中,不能改变主轴转速倍率开关。
* c7 l3 V& q+ h* H (3)应保证良好的冷却和润滑。 3 I5 m" M& G) V! @% r2 d) Y$ I
(4)车削低碳钢、不锈钢等材料时,会出现不易断屑的长条状切屑,应防止其卷入车刀和工件之间,使刀尖受挤压断裂。操作者必须注意人身安全。
. ?3 Y8 O2 b) `, H2 W8 C% B" G/ ] (5)需要中途换刀时,可待车刀返回到起刀点且尚未进给前,将主轴转速倍率旋钮调至“0”位。此时刀架停止,可以更换刀片。为方便操作,可在CYCLE97程序中可将APP值设大一些。
% `) W+ c9 W, g! G (6)在实际加工中,发生过因为打刀而使刀片和刀体一起损坏的情况,所以有必要增加一个刀位作为备用。需要注意:在对刀时必须保证这两个刀位上螺纹车刀刀尖点坐标一致,以免乱扣。 " x1 E: K1 t" D3 `# Z5 Z
2.打刀后的操作 & G; F2 ~$ C' A) `1 `3 \7 n( P% p
在沟纹辊16头螺纹车削过程中,粗车时分10次进刀,精车时分2次进刀,即每一头螺纹需要车刀沿 600×5210辊面往复12次,一共需要192次走刀。每次大约2分钟,有效车削时间总计约384分钟。在这样长的加工时间里,因为车刀磨损,切削力增大和辊面材料缺陷、焊缝区硬度变化等的影响,几乎每加工10到12头螺纹,就要打刀一次。打刀后我们可以按照以下步骤操作:
. O }' p) z8 ], K) C (1)待走刀结束并返回到起刀点再按“RESET”键停止(不能按“EMERGENCY”急停按钮,否则车刀会划伤辊面)。 % q+ f: R1 H* u: F5 U) H( @3 f+ x" g
(2)将碎刀尖从零件表面取出,否则在该位置会引起重复打刀。
+ x1 c$ L+ Y4 q1 ?/ S; l E, Z5 N (3)换刀后如果直接运行原程序,车刀又会从第一头螺纹开始加工,这样会浪费时间。我们可以调整CYCLE97程序中NSP值,改变第一头螺纹在辊体端面圆周方向上切入点的相位,使车刀从刚才打刀时的那头螺纹上开始加工。例如,打刀时正在加工的是第9头螺纹,如果原程序中NSP为0,那么换刀后NSP应为180,如图8所示。
& I5 x* N2 P* \/ g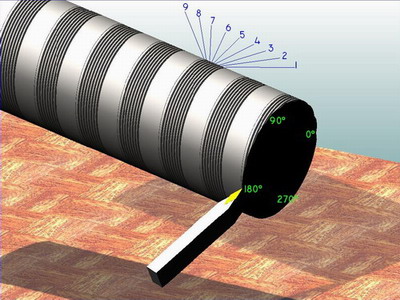
: D5 Z) @% s# m7 ^5 i图8
5 L& S6 ?1 w4 v* e# M1 M: }4 ? |